When operating asphalt pavers, a significant amount of material is moved through multiple moving parts to achieve the desired smooth pavement. However, not all of the asphalt ends up on the intended surface. Some of it can get stuck in different areas of the paver, and it is crucial to clear these areas before the asphalt hardens.
Compact pavers, especially those that perform various tasks throughout the day, are prone to asphalt buildup in their systems, leading to increased wear and unwanted periods of inactivity. Avoiding damage from buildup requires continuous attention throughout the entire workday, from the moment the paver is started up until it is shut down.
Buildup leads to breakdown of paver and paving quality
The accumulation of asphalt on the surfaces of an asphalt paver can quickly lead to various problems. This includes both mechanical issues with the machine itself and a decline in the quality of the pavement it is laying down, according to Chris Broome, Senior Product Manager at LeeBoy.
Broome explained that the excessive buildup of asphalt can cause increased wear on moving parts and any components that come into contact with the asphalt. As the material hardens, it can lead to binding of parts, further exacerbating the issue.
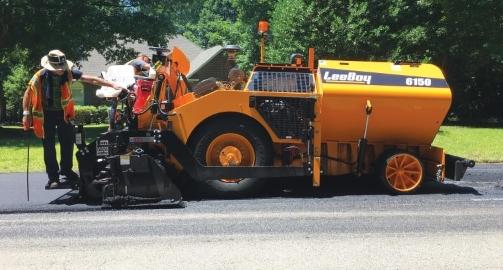
The accumulation of asphalt in a particular spot leads to further material buildup, which quickly impacts the operation of the asphalt paver. For instance, when there is buildup on the screed, it hinders the smooth movement of material and creates problems with the mat being laid.
The nature of compact pavers makes them particularly prone to asphalt buildup due to the way they are operated. In the competitive labor market of paving, it can be challenging to retain experienced employees on commercial crews, resulting in potential training gaps when it comes to activities like cleanup. As a result, pavers may neglect necessary cleaning, leading to issues that manifest the following day.
In contrast to highway-class pavers that typically focus on a single long-term project, compact pavers often move between multiple jobs throughout the day. This constant transition can result in cleaning challenges. Chris Broome explains:
“Some of these operators work on driveways, where they may complete two or three jobs in a day. As a result, you have asphalt buildup sitting on the machine for a couple of hours between jobs, which then hardens. While a full cleanup may not be necessary between each job, it is crucial for operators to take a moment or two to remove the hardened material.”
Start clean and stay clean
Ensuring the prevention of asphalt buildup on pavers begins from the moment the machine is new and should be maintained throughout its working lifespan. An important initial step is to thoroughly spray the paver with a release agent that is approved by local authorities. These water-soluble agents create a clean surface, acting as a barrier to prevent asphalt from sticking and accumulating on the paver. By implementing this practice, operators can effectively protect the paver from the onset of asphalt buildup.
“Prior to the initial job, it is crucial to thoroughly spray down all the fresh surfaces and paint of the paver,” emphasized Broome.
This includes lifting the deck in the case of wide conveyor pavers. The objective is to ensure that every area coming into contact with the asphalt receives a generous application of the release agent before the first load of mix is introduced to the machine. This meticulous step is of utmost importance to maintain the paver’s optimal performance and prevent asphalt buildup from the very beginning.
Ensuring the proper treatment of the surfaces is equally essential before commencing work each day. Experienced operators are typically aware of specific areas on their pavers that tend to accumulate asphalt buildup. It is crucial for them to proactively spray these spots with a release agent at the start of the day, as advised by Broome. This proactive measure helps to mitigate the risk of asphalt sticking to those areas and ensures smoother operations throughout the day.
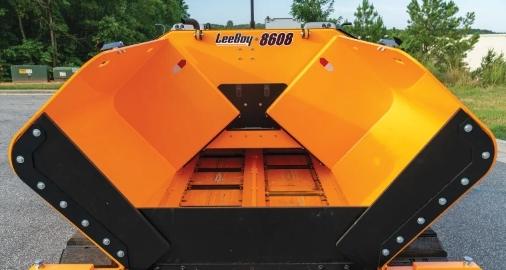
Throughout the day, it is crucial for crews to remain vigilant and watch for specific situations that can contribute to asphalt buildup. Overfilling the screed, for instance, can result in excess material being pushed over the top of the screed, where it can harden and cause issues. Similarly, when backing into a pile, there is a risk of picking up asphalt that may stick to the back of the screed. Additionally, in commercial paving operations, ground workers often use shovels to fill around utilities or other obstacles, which can lead to small spills that require prompt cleanup to prevent buildup. It is important for crews to address these situations promptly to maintain optimal performance and minimize potential issues.
It is essential to address spills promptly while the asphalt is still hot. If the spilled material is within reach, crew members should immediately knock it off the surfaces. In cases where the spill is not easily accessible, spraying it with a release agent is recommended. This will help prevent the asphalt from adhering and make it easier to remove at a later time. Taking these proactive measures ensures that the paver remains clean and minimizes the risk of asphalt buildup.
Wrap up the day with a good cleaning
To prevent asphalt from hardening overnight, it is crucial to thoroughly clean the pavers at the end of the day. Beginning with the conveyor, which comes into the most contact with asphalt throughout the day, is recommended by Broome.
To ensure effective cleaning, run the machine and activate the conveyors while spraying each individual bar as it moves. This is particularly important for pavers with wide conveyors where the bars move under the deck into the belly pans. This helps distribute the release agent and prevent material from fully hardening in that area. Additionally, it is recommended to move the conveyor after the cleaning process for about half an hour to prevent the bars from settling in any residual material that could cause resistance the next morning.
Broome recommends knocking off any excess material from both edges of the screed and spraying them down. It’s important to also extend the screed and check for any buildup. During the cleaning process, certain areas that are often overlooked can cause lingering issues. These include the wing hinges on either side of the hopper, particularly the space behind the hinge, which can be prone to asphalt buildup and potential damage. It’s crucial to inspect the tracks and walk boards as well, as they are often skipped during cleaning.
Control material to reduce buildup
LeeBoy has implemented design features in their compact pavers to prevent asphalt buildup. These features ensure the smooth movement of material throughout the machine, reducing the chances of buildup occurring.
LeeBoy incorporates a sonic sensor in their compact pavers to effectively manage the material height in the extension. Automatic controls are also employed to prevent asphalt from overflowing. By ensuring that the pile height is kept under control, the risk of overloading and subsequent issues, such as material getting between and under the tracks, is minimized. These sensors play a crucial role in maintaining optimal performance and preventing problems associated with asphalt buildup.
LeeBoy has implemented wing wipers in certain models, specifically located at the back of the wings where they intersect with the engine compartment. These wing wipers serve as protective measures to prevent material from escaping in that particular area. Broome emphasized the importance of using pavers equipped with additional controls that effectively keep the material in its intended place. Pulling an excessive amount of material that spills over the walk boards or toe board at the back of the paver can lead to numerous complications and challenges. Therefore, utilizing pavers with appropriate controls is essential for smooth operations and to avoid potential issues.